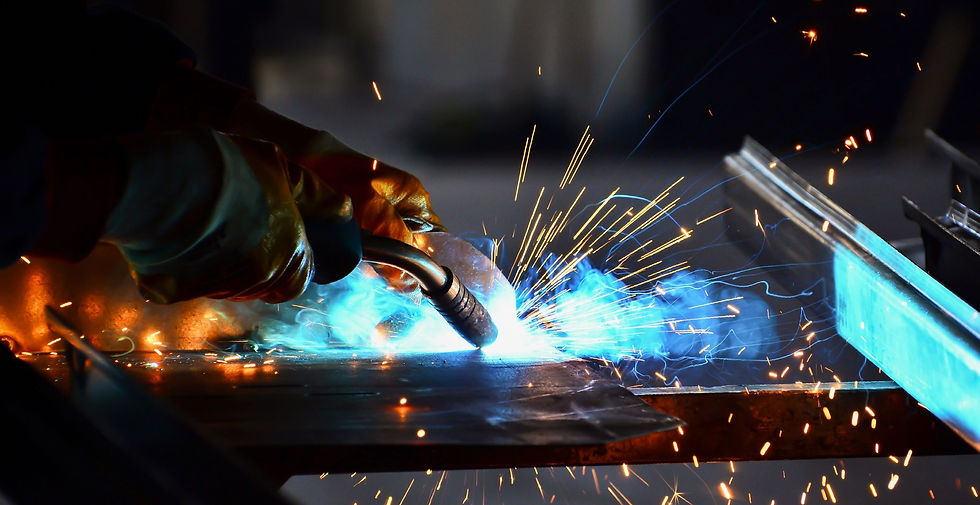
June 14, 2019 by Bob Wilson Welding might seem straight-forward, but the truth is that it is a very complicated process. It requires a knowledge of chemistry, patience, diligence, and a little bit of creativity. And welding different metals require different techniques and practices to achieve a neat and durable weld.
The importance of correct welding techniques and practices with different metals becomes apparent when we compare welding steel vs welding aluminium. Welders are used to welding steel and the techniques used for welding steel. But not following the correct techniques when you’re welding aluminium can lead to weak welds and a ton of wasted time.
In this article, we’ll go over aluminium welding vs steel welding, the different properties of each metal, and the different techniques and practices you should use when welding aluminium vs steel.
Aluminum Welding vs Steel Welding: Differences in Properties
To get an understanding of the differences between aluminium welding and steel welding, we need to get an understanding of the properties of each metal and how they are different.
Aluminium is much lighter and less dense than steel. It also has a much lower melting point. Aluminium melts at 1,221 degrees Fahrenheit, while steel melts at a temperature closer to 2,500 degrees Fahrenheit. That is more than double the melting temperature of aluminium. But aluminium has a trick up its sleeve. It also has an oxide layer on the outside that affects the melting temperature.
The melting temperature of the oxide layer is 3,700 degrees Fahrenheit, which is much higher than the melting point of the metal itself. The oxide layer is much harder than the aluminium and is meant to help the metal resist corrosion and wear. This oxide layer can cause issues when it comes to welding, such as arc start problems and issues with burn through on the base material.
Aluminium is also different from steel in the sense that it gets stronger as it gets colder. This makes it great for cold weather applications like transporting gasses. Steel gets more brittle and more prone to cracking as it gets colder, which is important to know during the welding process.
Differences During Welding
Due to the different properties of aluminium and steel, aluminium welding requires different techniques and practices to create strong welds.
Thermal Conductivity
Due to the fact that aluminium is lighter and less dense than steel, it has a thermal conductivity that is six times higher than steel. That means that the metal gets hotter much faster and also cools faster than traditional steel.
This can cause problems when it comes to the penetration of the weld and the depth of the weld. Because the aluminium quickly loses heat, this means the heat from the weld doesn’t go deep enough and can cause weak and incomplete welds.
When you are welding aluminium, you have to use much higher heat inputs to make sure that the weld penetrates deep enough to become effective. Make sure to pay attention to the thickness of the aluminium you are welding. Thicker pieces of aluminium will require even higher heat inputs and closer monitoring of the temperature of the metal.
Porosity
Another main difference between steel and aluminium welding is that aluminium is more susceptible to becoming porous. This is because hydrogen is very soluble in liquid aluminium.
As the aluminium is heated and turns to liquid, so does the filler material. Once they become liquid they begin to absorb hydrogen. And as the metal quickly cools down and becomes solid, hydrogen is no longer soluble. This creates small voids or “pores” in the weld, which weakens the weld and makes it prone to failure.
If you are welding aluminium, you must use a shielding gas that doesn’t have any hydrogen in it, such as pure argon gas. Using an oxy-acetylene torch or gasses that have hydrogen will cause porosity and weak welds.
Pre-Treatment of the Metal
Pretreatment of the metal you are welding is crucial to creating solid welds. Pretreatment of steel usually requires proper cleaning and removal of any residue or rust.
Pretreating aluminium before welding is a more involved process that takes longer and must get done in order to create effective welds.
The first step in pretreating aluminium is to make sure the metal is properly stored. If you are storing aluminium sheets outside, make sure to store them vertically. Stacking them horizontally can lead to water condensation, which is absorbed by the oxide layer and makes welding more difficult.
If you are storing your aluminium sheets outside, be sure to bring them into the shop a day before welding. This is so they can gradually come up to room temperature before welding. Welding cold aluminium leads to higher levels of hydrogen in the welds. This extra hydrogen leads to porosity and weakens the weld.
You should also clean aluminium with acetone or an aluminum cleaner before welding. This removes any dirt, oil, or residue that could cause defects in the weld.
But aluminium also requires an additional step. You’ll need to use a stainless steel wire brush to remove the oxide layer on the surface of the aluminium. This prevents burn through on your base material and prevents porosity, since the oxide layer can hold moisture, and therefore hydrogen.
Technique
While the weaving technique is great for welding steel, it shouldn’t be used for welding aluminium. Using a stringer bead instead of weaving will give you better penetration and fusion.
The higher thermal conductivity of aluminium also means you should use higher heat inputs to make sure the weld goes deep enough. You should also use a higher travel speed to stay ahead of the puddle of liquid aluminium and filler metal.
Proper Preparation Prevents Costly Mistakes
Learning the right techniques and practices for welding different kinds of metals will save you time and prevent you from making costly and dangerous mistakes. Make sure to research the different welding techniques to ensure you’re prepared for any welding job that comes your way. If you have any more questions about aluminium welding vs steel welding techniques, be sure to visit our blog.